Guía de Seguridad para Máquinas del Sector Madera. Parte 1
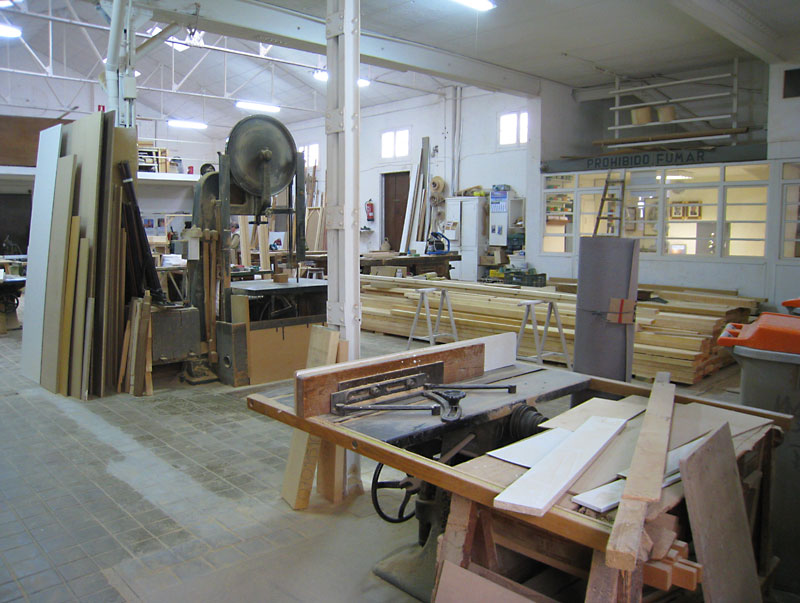
Edita y elabora: Foment del Treball Nacional oficinatecnica@foment.com
Con la financiación de: Fundación para la Prevención de Riesgos Laborales Con la colaboración de: Institut d’Estudis de la Seguretat (IDES) Con la participación: Gremi Fusta i Moble de Catalunya Autores: Bernardo Gutiérrez, Ingeniero técnico industrial Josep Maria Nadal, Ingeniero industrial Imágenes cedidas por: BARBERÁN- BOSTITCH – FELDER GROUP – HOMAG España – KOMMAD – MAKITA Código de acción: AT-0143/2015 Maquetación: Anglofort Reedición de la “Guía de seguridad para máquinas. Sector metal”, correspondiente al código de acción IT-0169/2013 (Acción solicitada y ejecutada por Foment del Treball con la financiación de la Fundación para la Prevención de Riesgos Laborales). El contenido de esta publicación es responsabilidad exclusiva de la entidad ejecutante y no refleja necesariamente la opinión de la Fundación para la Prevención de Riesgos Laborales. |
![]() |
---|
Guía de seguridad para máquinas del sector madera
Introducción
Desde la Oficina de Prevención de Riesgos para Pyme presentamos la tercera edición de la Guía de seguridad para máquinas, esta vez centrada en el sector de la madera. Para conseguir llevarla a buen puerto, hemos contado con la colaboración del Gremi Fusta i Moble.
Tanto para ellos como para nosotros es importante que los profesionales, en el caso que nos ocupa del sector de la madera, se impliquen en conservar su salud e integridad. Las máquinas son necesarias, el sueldo también, pero las manos de los profesionales todavía más, por eso es importante prestar atención a las indicaciones y recomendaciones que presentamos en este documento. Hay que evitar cualquier distracción, repasar de vez en cuando estas fichas y actualizar su contenido cuando sea necesario.
La formación, la información y la innovación expanden el buen oficio, pero nunca hay que olvidar que, de toda la cadena de producción, la única pieza que no tiene recambio son las personas. Este es el objetivo último de estos documentos: aumentar la seguridad de los trabajadores. Así ofrecemos una herramienta para conocer las máquinas y adecuarlas convenientemente.
En esta Guía el lector se va a encontrar con fichas de las siguientes máquinas: diferentes tipos de sierra, pistolas clavadoras, aplacadoras de cantos, regruesadoras, cepilladoras, lijadoras de bandas, barnizadoras de rodillo y tupís.
A nivel formal, siempre que ha sido posible, hemos intentado mantener el mismo orden de las ediciones anteriores en los apartados que desarrollan las fichas, para hacer una lectura más fácil y entendedora.
Para desarrollar esta Guía, Fomento ha confiado, de nuevo, en el Instituto de Estudios de la Seguridad, fundación privada, que ha realizado numerosas actuaciones sobre diferentes ámbitos de la seguridad desde su fundación en el año 1998. Los expertos redactores han sido los especialistas en la materia: Bernardo Gutiérrez, ingeniero técnico industrial y Josep Maria Nadal, ingeniero industrial. Creemos firmemente que la seguridad es el valor añadido. Por eso, y adaptando la frase de Derek Bok de «si crees que la formación es cara, prueba con la ignorancia», podríamos decir «si crees que la seguridad es cara, el accidente no tiene precio».
Las obligaciones legales
La Directiva 89/655 de 30 de noviembre de 1989, relativa a la utilización de los equipos de trabajo, transpuesta por el RD 1215/1997, prevé la puesta en conformidad de los equipos de trabajo en servicio en las empresas, a unos requisitos técnicos de seguridad.
La puesta en conformidad de los equipos de trabajo, debe ser una parte fundamental de la evaluación de riesgos de la empresa, una oportunidad para el director de la fábrica para conocer el estado de sus equipos de trabajo y una buena base para mejorar el aspecto organizativo de la producción.
La correcta aplicación de esta legislación dará como resultado una sensible disminución de los incidentes y/o accidentes de trabajo en la empresa.
Es a esta finalidad a la que hemos dedicado este trabajo fruto de muchos años de dedicación a esta apasionante y novedosa rama de la ingeniería que es la seguridad de los equipos de trabajo y, en particular, de las máquinas.
En el año 2000, el INSHT publicó la Guía técnica para la evaluación y prevención de los riesgos relativos a la utilización de equipos de trabajo. Esta Guía, aún siendo de carácter no vinculante, facilita la aplicación del RD 1215/1997 al ampliar todos y cada uno de sus apartados.
En el apéndice A, «Disposiciones aplicables a las máquinas», se definen los períodos de aplicación de todas las disposiciones aplicables a las máquinas, en relación con la primera comercialización y/o puesta en servicio. De la lectura de dicho apéndice y de la figura que le acompaña, se deduce que el RD 1215/1997 se aplica a las máquinas que fueron comercializadas y/o puestas en servicio con anterioridad al 1 de enero de 1995.
La Guía del INSHT, en su página 16, afirma que «Los requisitos fijados en el anexo 1 del RD 1215/1997 tienen poca concreción. Por el contrario, las directivas relativas a la comercialización de productos establecen niveles elevados de seguridad, se aplican a productos (y riesgos) específicos y fijan (directa o indirectamente) requisitos mucho más concretos. Consecuentemente, en la práctica, el anexo I es de aplicación subsidiaria respecto a la citada normativa y debe suponerse que los equipos de trabajo sujetos al marcado CE (máquinas, equipos médicos, aparatos de gas, equipos a presión, etc.) lo cumplen siempre. La simple aplicación de los requisitos de este anexo I a equipos con reglamentación específica (en el caso de las máquinas, a las posteriores al 1 de enero de 1995) podría suponer una merma en los niveles de seguridad exigibles y puede que no satisfagan lo requerido por el estado de la técnica.» Es muy recomendable que en el momento de la compra de máquinas, el empresario se asegure de que el Marcaje CE es correcto.
La aplicación de la directiva de máquinas y, por ende, de las nomas europeas armonizadas, exige unos niveles de seguridad más exigentes que la aplicación de los requisitos establecidos en el RD 1215/1997.
Por lógica, el paso del tiempo irá haciendo desaparecer las máquinas más antiguas, siendo estas sustituidas por otras de nueva construcción con unos niveles de seguridad más elevados. Este proceso nos llevará a una disminución de los accidentes en máquinas, que es lo que pretende esta legislación sobre seguridad que se ha ido publicando en estos últimos años.
Aspectos generales
RD 1215/1997, Anexo 1.1, Apdo. 1:
«Los órganos de accionamiento de un equipo de trabajo que tengan alguna incidencia en la seguridad deberán ser claramente visibles e identificables y, cuando corresponda, estar indicados con una señalización adecuada. |
---|
En este apartado de la Guía, se relacionan los diecinueve apartados del Anexo I del Real Decreto 1215/1997 en el mismo orden en el que aparecen en dicho Real Decreto.
En cada uno de estos apartados, después de citar el texto que aparece en la norma, los expertos describen los criterios fundamentales de tipo general que deberán aplicarse a cualquier máquina, cuando el apartado le sea de aplicación.
3.1 Órganos de accionamiento
Los órganos de accionamiento del equipo, que tienen alguna incidencia en la seguridad, deben ser claramente visibles e identificables y, cuando corresponda, estar indicados con una señalización adecuada. Se recomienda el siguiente código de colores:
- Puesta en marcha: BLANCO (se acepta el verde en máquinas antiguas).
- Paro: NEGRO (se acepta el rojo en máquinas antiguas).
- Paro de emergencia: ROJO sobre fondo amarillo.
- Rearme: AZUL.
Los órganos de accionamiento1 deben estar situados fuera de las zonas peligrosas. Excepcionalmente, si es necesario realizar operaciones dentro de una zona peligrosa, habrá que cumplir los siguientes requisitos:
- Utilizar un modo de mando específico en la máquina que anule el resto de modos de mando.
- Los elementos peligrosos solo deben funcionar si se actúa permanentemente sobre un dispositivo de validación2, un mando sensitivo3 o un mando a dos manos4.
- Autorizar, únicamente, el funcionamiento de los elementos peligrosos en condiciones de riesgo reducido (velocidad reducida, movimientos paso a paso, etc.)
- Cumplir con, al menos, una de las siguientes medidas preventivas:
a) Máxima restricción posible de acceso a la zona peligrosa,
b) Paro de emergencia al alcance inmediato del operador; o
c) Botonera de mando portátil, como único mando activo.
Los órganos de accionamiento no deben acarrear riesgos como consecuencia de una manipulación involuntaria. Es aconsejable el uso de pulsadores enrasados, o con anillo de protección. En caso de pedales, deben estar cubiertos y cerrados lateralmente.
El operador del equipo debe poder cerciorarse, desde el puesto de mando principal, de la ausencia de personas en las zonas peligrosas. Si esto no es posible, las zonas fuera del control del operador deben estar cerradas perimetralmente y, si disponen de accesos, estos deben estar dotados de enclavamientos. Es recomendable que el rearme de cada acceso se realice localmente, y que haya disponible un paro de emergencia5 en el interior de estas zonas. Si no es posible usar estas medidas, se recomienda instalar un aviso acústico y/o visual que se active automáticamente antes de que ocurran los movimientos peligrosos y cuya duración garantice la evacuación de las zonas peligrosas. Si aun así no se puede garantizar que estén despejadas las zonas peligrosas, hay que instaurar un procedimiento de trabajo que lo asegure.
Los órganos de accionamiento relativos a la seguridad (como paros de emergencia5, dispositivos de enclavamiento6, barreras fotoeléctricas7, mandos a dos manos, etc.), deben tener una fiabilidad acorde al riesgo que protegen. Se recomienda seguir las indicaciones de la norma pertinente.
RD 1215/1997, Anexo 1.1, Apdo. 2:
«La puesta en marcha de un equipo de trabajo solamente se podrá efectuar mediante una acción voluntaria sobre un órgano de accionamiento previsto a tal efecto. |
---|
3.2 Puesta en marcha
Solo debe ser posible efectuar la puesta en marcha del equipo de trabajo mediante una acción voluntaria sobre un órgano de accionamiento previsto a tal efecto. En caso de cambio del modo de funcionamiento de la funcionalidad de la máquina, este debe ser realizado voluntariamente por el operador y debe requerir una nueva puesta en marcha.
Tras una parada, se debe asegurar que la nueva puesta en marcha se realice de forma voluntaria. La máquina no se debe poner en marcha en los siguientes casos:
- Por el cierre de un resguardo8 con dispositivo de enclavamiento
- Por la liberación de un dispositivo sensible9, como una barrera fotoeléctrica
- Por el cambio en un selector de modo de funcionamiento
- Por el desbloqueo de un paro de emergencia
- Por un rearme
Excepcionalmente, se permite que un resguardo con enclavamiento o un dispositivo sensible autoricen una puesta en marcha, si se cumplen los siguientes requisitos:
- Que sea imposible permanecer en la zona peligrosa al cerrar el resguardo o atravesar el dispositivo sensible.
- Que el resto de resguardos estén cerrados y rearmados.
- Que, si el riesgo que se está protegiendo puede causar lesiones graves, el sistema de mando sea de alta fiabilidad, según la norma pertinente.
RD 1215/1997, Anexo 1.1, Apdo. 3:
«Cada equipo de trabajo deberá estar provisto de un órgano de accionamiento que permita su parada total en condiciones de seguridad. |
---|
3.3 Parada y parada de emergencia
El equipo debe estar provisto de un órgano de accionamiento que permita su parada total en condiciones de seguridad.
Si el equipo dispone de más de un puesto de mando, cada uno debe estar provisto de un órgano de accionamiento que permita hacer un paro, total o parcial del equipo, ante una situación de peligro.
La orden de parada del equipo de trabajo debe tener prioridad sobre las órdenes de puesta en marcha.
La orden de parada del equipo de trabajo debe interrumpir el suministro de energía de los órganos de accionamiento o de sus elementos peligrosos una vez obtenida la parada del equipo de trabajo.
El equipo debe tener un dispositivo de parada de emergencia en función de los riesgos que presenta el equipo de trabajo y del tiempo de parada normal. El paro de emergencia solo tendrá sentido cuando reduzca efectivamente el tiempo de parada normal. Esto no implica la obligatoriedad de instalar un sistema de frenado en el equipo, únicamente se debe instalar si el riesgo es alto. Por ejemplo, no es necesario instalar un sistema de frenado en una esmeriladora.
Están permitidas las siguientes formas de parada para el dispositivo de parada de emergencia:
- Parada inmediata: interrupción inmediata de energía sobre todos los accionadores.
- Parada controlada: los accionadores necesarios permanecen en tensión para llevar al equipo a un estado de parada segura, y luego se interrumpe la energía sobre todos los accionadores.
El órgano de accionamiento del paro de emergencia puede ser: - Pulsador tipo «seta».
- Cable (con la condición de que al cortarlo, se desencadene la parada de emergencia).
- Barra.
- Pedal (en este caso sin caperuza de protección).
RD 1215/1997, Anexo 1.1, Apdo. 4:
«Cualquier equipo de trabajo que entrañe riesgo de caída de objetos o de proyecciones deberá estar provisto de dispositivos de protección adecuados a dichos riesgos». |
---|
3.4 Caída de objetos y proyecciones
Se deben tomar medidas para evitar que se puedan producir accidentes por la caída o proyección de:
- Material relacionado con la producción: virutas, chispas, fluidos, partículas, etc.
- Partes móviles del equipo: herramientas giratorias, ejes, contrapesos, etc. Las medidas preventivas a tomar son:
- Resguardos que tengan la resistencia suficiente para retener dichas caídas o proyecciones.
- Evitar puestos de trabajo en la trayectoria de dichas caídas o proyecciones.
- Impedir que se pueda circular por las zonas de trayectoria de dichas caídas o proyecciones, mediante barandillas, protecciones u otros medios.
- Instalación de sistemas de frenado, de bloqueo, sistemas paracaídas o válvulas antiretorno, en los equipos de elevación de cargas que eviten la caída de las cargas, incluso en el caso de que se produzcan cortes de energía imprevistos.
RD 1215/1997, Anexo 1.1, Apdo. 5:
«Cualquier equipo de trabajo que entrañe riesgo por emanación de gases, vapores o líquidos o por emisión de polvo deberá estar provisto de dispositivos adecuados de captación o extracción cerca de la fuente emisora correspondiente». |
---|
3.5 Emanación de gases, vapores o líquidos y emisión de polvo
Se debe evitar la exposición de los trabajadores a sustancias peligrosas por emisión de gases, vapores, líquidos o polvo. Se debe evaluar la peligrosidad de las sustancias emitidas, la intensidad de la emisión y las condiciones de trabajo.
Hay que solicitar al proveedor habitual la «Ficha de seguridad» de los productos que utiliza el equipo. Si los productos son peligrosos10: irritantes11, sensibilizantes12, fibrogénicos13, asfixiantes14, tóxicos15, carcinógenos16, infecciosos17, etc.; se deberán tomar medidas de las concentraciones de los contaminantes en los puestos de trabajo
y compararlos con los valores VLA18 para comprobar si existe riesgo de contraer una enfermedad profesional.
Si la evaluación requiere medidas preventivas, será necesario instalar un sistema de captación y extracción. Podría ser necesario tomar otras medidas complementarias como: ventilación, organización del trabajo y, como último recurso, la protección individual.
RD 1215/1997, Anexo 1.1, Apdo. 6:
«Si fuera necesario para la seguridad o la salud de los trabajadores, los equipos de trabajo y sus elementos deberán estabilizarse por fijación o por otros medios. Los equipos de trabajo cuya utilización prevista requiera que los trabajadores se sitúen sobre los mismos, deberán disponer de los medios adecuados para garantizar que su acceso y permanencia en esos equipos no suponga un riesgo para su seguridad y salud. En particular, cuando exista riesgo de caída de altura de más de 2 metros, deberán disponer de barandillas rígidas de una altura mínima de 90 centímetros, o de cualquier otro sistema que proporcione una protección equivalente». |
---|
3.6 Estabilidad y medios de acceso y permanencia
Hay que fijar adecuadamente el equipo de trabajo según indique el manual de instrucciones del fabricante; asimismo, también deberá estar nivelado. Habrá que tener en cuenta el tipo de fijación para que esta no transmita vibraciones.
Comprobar que las condiciones de acceso a un equipo de trabajo son seguras, tanto si se realizan con medios de acceso móviles (andamios, escaleras de mano, etc.), como si se realizan con medios de acceso fijos (escala, escalera, rampa, pasarela, etc.)
Andamio:
Es importante para estos elementos seguir las instrucciones de montaje y mantenimiento indicadas por el fabricante, y en su caso redactar el preceptivo proyecto, para evitar dichos riesgos.
Si supera los 2 m. de altura, necesitan un acceso desde el interior mediante trampilla y que las ruedas tengan un dispositivo de fijación para evitar cualquier movimiento involuntario.
Tendrá especial consideración el hecho de que la base sea estable (ruedas fijadas, el andamio debe estar a nivel).Escala:
Medio de acceso fijo con un ángulo de inclinación superior a 75°, hasta 90°, cuyos elementos horizontales son escalones. A partir de los 2,20 m. de altura irá provista de una jaula de seguridad.Escala de peldaños:
Medio de acceso fijo con ángulo de inclinación superior a 45°, hasta 75° cuyos elementos horizontales son peldaños.Escalera:
Medio de acceso fijo con un ángulo de inclinación superior a 20°, hasta 45°, cuyos elementos horizontales son peldaños. La huella (g) y la contrahuella (h) deben respetar la fórmula: 600 <g+2h<660 (dimensiones en mm.)Rampa:
Medio de acceso fijo constituido por un plano inclinado continuo con un ángulo de inclinación superior a 0°, hasta 20°.Pasarelas:
La altura libre entre el techo y el suelo de la pasarela debe ser de 2.100 mm. La anchura mínima de una pasarela, excepto en circunstancias excepcionales, será de 800 mm. Las aberturas máximas del suelo, deben ser tales que no pueda pasar una esfera de 35 mm. de diámetro. La superficie del suelo debe estar diseñada para reducir el riesgo de resbalar.Barandillas:
El pasamano de las barandillas tendrá una altura mínima de 1.100 mm. respecto al suelo. Tendrá un travesaño a 600 mm. del suelo y un rodapié de 100 mm. de altura mínima.
RD 1215/1997, Anexo 1.1, Apdo. 7:
«En los casos en que exista riesgo de estallido o de rotura de elementos de un equipo de trabajo que pueda afectar significativamente a la seguridad o a la salud de los trabajadores, deberán adoptarse las medidas de protección adecuadas». |
---|
3.7 Estallidos o roturas
En general el riesgo será consecuencia de la rotura de una herramienta, una tubería por fluidos, un golpe recibido o diferentes tipos de desgaste como la fatiga o la corrosión, por ejemplo.
Los resguardos y las conducciones de fluidos deben resistir los impactos previstos por el fabricante tanto por masa como por velocidad del objeto o del material proyectado, así como la resistencia de las uniones y puntos de fijación usados en estos (en caso necesario, hay que tener en cuenta los requisitos del apartado 8). Las máquinas con herramientas rotativas deben disponer de las correspondientes protecciones, pero si estas no son suficientes, además, deberán:
- Evitar que sobrepase el régimen de velocidad establecido por el fabricante, en función del material.
- Seguir las instrucciones del manual de instrucciones del equipo de trabajo en cuanto a las revisiones de mantenimiento para conocer los ajustes de herramientas, desgaste y sustitución.
Para los equipos de trabajo que funcionen automáticamente con un movimiento del material hacia la herramienta solo entrarán en contacto herramienta y pieza cuando hayan alcanzado las condiciones normales de trabajo.
El movimiento de la herramienta y de la pieza estará coordinado cuando se efectúe tanto la puesta en marcha como una parada tanto si se realiza de forma voluntaria como involuntaria.
RD 1215/1997, Anexo 1.1, Apdo. 8:
«Cuando los elementos móviles de un equipo de trabajo puedan entrañar riesgos de accidente por contacto mecánico deberán ir equipados con resguardos o dispositivos que impidan el acceso a las zonas peligrosas o que detengan las maniobras peligrosas antes del acceso a dichas zonas. |
---|
3.8 Elementos móviles
Los sistemas de protección existentes y sus características son:
- Resguardo fijo: protección que solo se puede retirar con el uso de una llave o herramienta.
- Resguardo móvil: protección que se puede abrir sin utilizar herramientas. Este tipo de protección siempre irá asociado a un sistema de enclavamiento o enclavamiento y bloqueo.
– Resguardo con enclavamiento: el resguardo se puede abrir en cualquier momento del proceso y el sistema de enclavamiento da la orden de parada (es seguro si en el momento de acceso no hay órganos en movimiento).
– Resguardo con enclavamiento y bloqueo: el resguardo permanece bloqueado en posición de cerrado hasta que hayan desaparecido las funciones peligrosas. - Resguardo regulable: protección móvil ajustable que una vez ajustado mantiene la posición y no lleva asociado otro sistema de seguridad.
- Dispositivo de protección sensible: equipo para detectar personas o partes de personas, que genera una señal apropiada al sistema de mando con el fin de reducir el riesgo para las personas detectadas (barreras fotoeléctricas, alfombras sensibles, escáneres, etc.). INCONVENIENTE: no protegen ante algunos riesgos como la proyección de objetos, líquidos o movimientos con energías residuales.
Selección en función del acceso
Elementos móviles de transmisión: Como la mayoría de las veces el acceso a estos elementos es ocasional, con un resguardo fijo, será suficiente. En caso de que existan movimientos inerciales, se pueden poner tornillos de rosca más largos, para alargar el tiempo de apertura, o un sistema de enclavamiento con bloqueo.
Elementos móviles en la zona de trabajo: En la mayoría de los casos se instalará un resguardo móvil asociado a un sistema de enclavamiento o enclavamiento y bloqueo, o bien un sistema de protección sensible.
Los resguardos con cierre automático deben estar provistos de un borde sensible que evite los posibles atrapamientos.
Selección en función de la frecuencia
Esporádico (menos de una vez por turno): resguardo fijo o móvil con enclavamiento.
Frecuente (más de una vez por turno): resguardo móvil con enclavamiento o enclavamiento y bloqueo o dispositivos de protección sensible (barreras fotoeléctricas, alfombras, etc.).